自 2010 年开始,江苏和浙江一带的相关制药企业*先开始对生产过程中的废气进行治理,当时的治理重点在对异味的治理。治理工艺如三级喷淋技术“碱洗+催化氧化+水洗”的老三段工艺。这是早期的发酵尾气处理工艺。2014—2015 年,江浙一带的相关药企已经将蓄热式热力焚烧(RTO)、蓄热式催化焚烧(RCO)等技术用于VOCs终端治理。京津冀的制药企业从 2014 年起开展了异味治理。进入“十三五”之后,制药行业 VOCs 和异味治理工作全面铺开。2019年,国家颁布《挥发性有机物无组织排放控制标准》(GB 37822-2019)、《制药行业大气污染物排放标准》(GB 37823-2019)2 个标准,要求现有制药企业要在 2020 年 7 月起执行新标准。因此,相关制药企业废气的达标排放还将面临很大挑战。
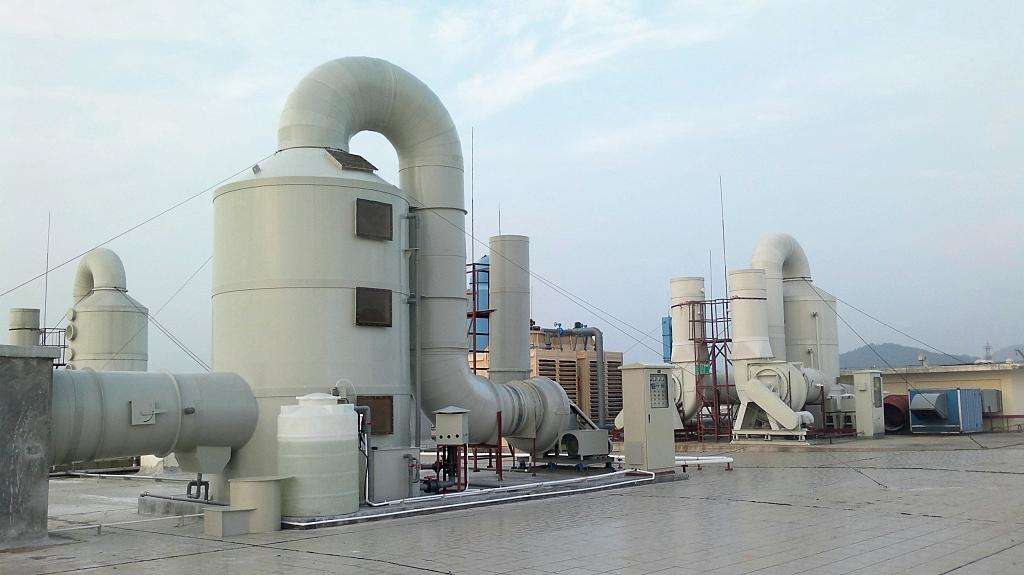
1)企业对VOCs 治理技术的选择缺乏针对性。由于原料药产品繁多,所用生产原料种类多、VOCs 排放环节多,而且不同生产工序的废气特点各异(有机物成分、浓度、风量等均不同),因此,没有一种技术能够处理所有的废气。各制药企业根据自身特点在不断完善治理工艺,但仍需要一定的摸索时间。例如,制药企业常见的碳纤维吸附技术,企业在引进时以“多级冷凝+碳纤维吸附”工艺为主;但实际应用中,在碳纤维再生干燥阶段会出现高浓度VOCs 溢出,设施尾气可能会超过100 mg·m-3;企业对这些尾气只能再实施收集冷凝处理,使排气VOCs 稳定在60 mg·m-3以下,或直接将碳纤维吸附段的排放尾气引致RTO、RCO 中焚烧处置,使排气VOCs 浓度稳定在8 mg·m-3 以下。另外,企业在可行性治理技术选择方面,还应综合考虑处理效率、运行成本和二次污染等。一些废气治理技术在应用过程中产生臭氧和有机中间产物等二次污染物,需要企业进一步分析二次污染的风险及其削减措施才可考虑使用。例如,低温等离子体、光催化氧化技术应用过程中会产生相当大量的臭氧;而青霉素生产中常用的乙酸丁酯和正丁醇在气相降解过程中会产生100 多种中间产物。
2)不能直接照搬其他行业的治理技术。目前,在 VOCs 治理领域,国家正陆续研究并出台相关技术规范,但不同行业的企业在选择废气治理技术上还处于试验和摸索期。制药行业也不能直接照搬其他行业的可行技术。例如,在石化行业应用较好的 VOCs焚烧处理方法,并不适合处理原料药生产的发酵、结晶、精制等工序中排放的大风量、低浓度废气或是间歇性排放 VOCs治理。
3)企业对无组织废气收集不足。无组织废气收集不足表现在两个方面:一方面,VOCs 无组织收集点位不足。尽管企业对于废气的收集与处理意识在逐步提高,从*早的针对发酵尾气、真空泵尾气等有组织废气治理,到对主要溶媒储罐溢散口废气收集,但对于车间密闭管理、对所有涉及 VOCs物料投加口、冷凝器出口、实验室废气、危废库房的废气收集与治理仍不足;另一方面,废气收集系统的设计还有待优化。对于一个高效的废气治理系统而言,废气收集及输送系统设计是整个系统中极其关键的部分。目前,部分企业在增加无组织收集措施时,存在收集气体 VOCs浓度过低、风量过大,造成后续废气治理设施能力不足或增大处理成本,给废气末端高效净化带来了很大压力。
4)企业废气排放自行监测能力不足。对于制药企业,从安全、职业卫生方面考虑,现场废气检测设备有甲烷、硫化氢、一氧化碳、丙酮、臭气浓度等便携式检测设备或速测管,而对于多组分挥发性有机废气的便携式检测设备则
比较少。另外,以氢火焰离子化检测器( flame ionization detector,FID)检测非甲烷总烃的便携式和固定源在线监测设备费用高,国产固定源在线监测设备售价是 COD在线监测设备的 4 倍。大部分企业使用较多的是 TVOC 检测和报警设备。此类设备以光离子监测(PID)方法为主,无国家技术规范。尽管这类设备费用低,但维修频次高,设备检测误差大。另外,VOCs 在线设备的第三方运维公司较少,不同于废水COD、氨氮在线监测设备的第三方运行模式已经成熟和规范。故企业面临废气设备检测因子少、设备费用高的问题。针对上述问题,企业需建立自己的废气监测实验室、配备相应监测人员,并根据内部物料平衡、内部实测等方法,排查重点排污点源,委托有资质的单位进行定期监测,确保企业能及时掌握排污状况。
版权声明:本网注明来源为“乐发环保”的文字、图片内容,版权均属本站所有,如若转载,请注明本文出处:http://www.keketie.com 。同时本网转载内容仅为传播资讯,不代表本网观点。如涉及作品内容、版权和其它问题,请与本网站联系,我们将在及时删除内容。