炼化行业生产过程中的VOC废气污染在国内外均属于*严重的空气污染物质之一,大量的VOC废气使得人们的生命安全受到严重影响,炼化行业必须加强VOC废气处理技术的研究与应用,提高该类废气处理效率。
VOC废气当前的处理技术主要分为两种,一个是回收,一个是销毁,不同的处理技术能够达到不一样的处理效果,且对VOC废气的组成成分要求也存在差异,实际处理工作中,还应该根据处理标准与VOC废气的成分来合理的选择,保证VOC废气处理的科学性,提高其净化质量。
近年来,随着人们对大气污染重视程度和政府部门大力的治理,周边环境有了明显好转和改善。在对环境治理的同时,日常提到*多是PM2.5、VOC,其中VOC即易挥发的有机化合物(VolatileOrganicCompounds),具体是指在标准大气压101.3kPa下初沸点小于或等于250℃且能对视觉感官产生刺激危害的有机化合物。
首先VOC会对健康产生不良影响,由于VOC一般以气态存在,所以对有毒害性VOC气体的处理与不易挥发的混合物相比更加困难。人体可能通过接触或食用摄入固态或液态有VOC成分的物质,或者吸入的气体接触到VOC等。
1炼化行业中的VOC废气概述
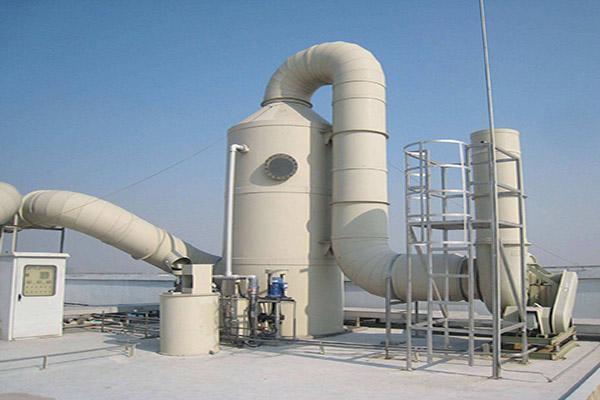
1.1 VOC废气的含义
VOC废气也被叫做挥发性有机污染气体,这是由于其中含有大量的易挥发性有机物而得名,其暴露在空气中后会与大气发生光化学反应而形成有机化合物,主要的化学物质为含氧、氮、氯、硫、甲烷烃等类有机物,是导致臭氧污染以及形成PM2.5污染物的重要物质。
1.2 VOC废气的主要形成环节
炼化行业的生产过程中,形成VOC废气的环节较多,多数分散在各个生产环节中,其中的主要形成环节有以下几点:
①化工厂中的有机液体储罐区域内,这是由于“大呼吸”与“小呼吸”的影响而形成挥发性气体;
②容易散发出VOC废气的生产环节中,例如化工合成、过滤、蒸馏、离心等生产工序中,都极易出现VOC废气;
③生产车间中进行物料转移的过程,在将物料从第*个储存器转移到第二个储存器中时,也会存在吸入气体与放出气体的过程,从而形成VOC废气;
④生产环节中发生泄露情况,生产设备的长时间使用而出现的腐蚀以及磨损,没有及时采取养护办法等,进而导致物料泄露的情况发生;
⑤生产管理机制缺失,由于生产过程中的管理机制不完善,操作人员存在错误操作的情况,导致有机物质发生泄露或非正常的排放等等。
1.3 VOC废气带来的主要危害
首先,VOC废气暴露在空气中会严重影响空气质量,当人体吸入受到污染的空气时,就会给其肺部功能产生影响,长期且大量的吸入VOC废气,还可能导致人体细胞发生癌变,*终导致癌症疾病。另外,VOC废气在空气中产生光化学反应后,会形成雾霾,使得人们的视野范围遭到遮挡,给人们的正常工作和出行带来严重影响。
2VOC 末端处理技术
VOC末端处理技术可分为回收处理及氧化处理两大类和它们的结合应用。
2.1回收处理技术
回收处理VOC技术包括冷凝、膜分离、吸附、吸收等。为了获得具有足够纯度的有机物,在利用吸附、吸收和接触式冷凝等方法使气相VOC转移至固相或液相之后,还需要借助热解析、气提、精蒸馏等手段分离有机组分。
2.1.1冷凝法
冷凝回收法是利用有机物在不同温度下,其饱和蒸气压不同,通过冷凝器降温或升压,使有机物冷凝成液体,从气相中分离出来。冷凝提取后,有机废气便可得到比较高的净化。*通用的冷凝方法有表面冷凝和接触冷凝。
冷凝法主要应用于高浓度VOC气体处理,尽管在理论上可达到很高的净化程度,但是其操作难度大,难于在常温下用冷却水来完成,需要给冷凝水降温,当浓度低至每升数百毫升时,处理成本会大大提高。所以冷凝法常作为吸附、膜分离或者其他VOC深度净化方法的前处理措施,以回收有机物,并降低后续处理的负荷。
2.1.2膜分离法
不同气体分子通过具有选择性的膜时,其扩散渗透率不同,在膜两侧施加推动力时,有机选择渗透膜将气体分成2种物流,不能通过膜的气体为脱除了VOC的洁净空气被排放,通过膜的有机气体继续被循环冷凝。
膜分离法回收VOC就是借助真空泵,在纳米级的气体分离膜两侧形成压力差,使得VOC气体透过膜,而空气透过膜的速率小得多,通常高分子膜对VOC的速率比空气高10~100倍。膜分离法主要应用于浓度在1000mg/m3以上的VOC气体回收处理,回收率能够达致90%~99.9%。
膜分离法*大的优点运化效果好,无二次污染物,回收的VOC无须后续处理。但是,膜处理技术投资运行费用高,且污染的膜被丢弃后会造成污染。分离的效率可能会受到诸如腐蚀性气体、含尘气体或气体接近露点等的影响。
2.1.3吸附法
吸附法去除有机物是利用比表面积大,具有多孔结构的活性炭、碳纤维、沸石等吸附剂,将有机物分子截留,当废气通过吸附床时,有机物就被吸附在孔内,使气体得到净化。吸附法主要适用于风量大、湿度低、温度低、浓度小于5000ppm的VOC气体的回收处理。VOC吸附效果的影响因素很多,吸附剂本身的物理性质、化学性质、VOC的分子结构、外界环境的温度、湿度及共存污染物等都会影响吸附法的工艺性能。
2.1.4吸收法
吸收法有物理和化学吸收两种途径。物理吸收法是利用物理性质差异进行分离。根据相似相溶和溶解度原理,吸收剂一般选用与挥发性有机物性质相近的非极性或弱极性液体,沸点高、挥发性低且化学性质稳定,能够长期使用。
常用的吸收剂有以柴油和洗油为主的矿物油、水型复合溶剂(例如水-洗油、水-表面活性剂-助剂)及高沸点有机溶剂。除易溶于水的有机挥发性气体以水或液相有机物为溶剂进行物理吸收外,其他情况以酸液、碱液为溶剂进行化学吸收。
2.2 氧化处理技术
氧化处理VOC技术包括直接燃烧、热力燃烧和催化燃烧等热氧化技术以及生物过滤、生物滴滤和生物洗涤等生物降解技术等。
2.2.1直接燃烧技术
直接燃烧也称直接火焰燃烧,是将废气中VOC组分当作燃料的处理方式,因此该法只适用于VOC浓度或热值较高的废气,其燃烧温度通常维持在1100℃左右。该方法主要处理浓度较高,不回收利用的回收系统循环吸收。
2.2.2催化燃烧
催化燃烧是气相和固相催化反应,催化剂一般使用铂、钯等贵金属。催化剂降低了分子的活化能,提高了反应速率,使废气无焰且低启燃条件燃烧。是目前主流的废气处理途径,但有催化剂采购昂贵和易受废气中硫含量影响中毒的缺点。
2.2.3生物处理技术
生物降解技术适合低浓度的VOC介质,通过控制细菌的碳源平衡,维持细菌组成和数量保证一定的污染物去除率,具有无二次污染的优点,但必须维持处理环境的稳定。
2.3超低含氨废气处理的示例
在进入氨气回收系统前对RO纯水经过制冷系统冷却至4~6℃,从膜吸收组件吸收液入口进入气态分离膜组件。每级氨气回收系统配20支气态分离膜组件,每支气态分离膜组件膜壁孔径为0.0001~20μm,吸收面积为105m2,并联排列。
氨气回收系统入口风压控制在35~40kPa,气态分离膜为中空纤维微孔膜,废气和冷冻纯水分别在膜的两侧,氨气透过膜孔被另一侧的冷冻纯水所吸收进入吸收液。气态分离膜亲气而疏水,氨气从膜的极微小的孔径内透过进入另一侧的吸收液中,而吸收液却不能进入氨气流动一侧。
氨气回收系统中,各路流体的状态参数均通过传感器转送至自动控制系统,控制系统根据回传的信号进行相应的调整,保证系统处于稳定的工作状态。氨气与低温的纯水相遇迅速溶于水中形成稀氨水后进入吸收液箱,同时产生大量的反应热。
本工艺中设有五级吸收氨气的吸收液箱,在第五级吸收液箱是*浓的,当第五级吸收液箱达到浓度时自动排放到氨水储槽,此时第四级吸收液箱内的还未达浓度要求的氨水会通过五级液位传感器发出的低液位信号控制电动三通阀切换排入第五级吸收液箱进行进一步吸收以增加浓度。
由此方式第三级排入第四级,第二级排入第三级,依次进行。多级膜吸收组件的吸收液经多次循环后,可以达到20%以上的浓度品格,作为成品氨水引出。再补充纯水,重复以上步骤。
由于气态分离膜系统预先去除了大部分氨,总去除效率达99%,剩余1%的超低含氨废气从膜吸收组件下方排出,接入尾气吸收酸池。经吸收酸池吸收后尾气中氨浓度极低,可以稳定达标排放。
综上所述,VOC废气的排放不满足净化标准时,将会在大气中发生光化学反应,形成PM2.5,影响人们的视线范围。另外,人体长期吸入大量的VOC气体,还会导致呼吸道与肺部的感染,严重时可能导致机体细胞的癌变,给人们的生命安全构成威胁。
因此,必须采取合理有效的治理手段,使得VOC废气中的有害物质被成功消除或减少,降低VOC废气给环境带来的危害。回收与销毁是当前的VOC废气中比较常用的两大处理技术,在实际的应用中,需要根据废气物质的具体组成以及处理目标的差异进行科学选择,使得VOC废气的净化效果得到*大程度提高。
版权声明:本网注明来源为“乐发环保”的文字、图片内容,版权均属本站所有,如若转载,请注明本文出处:http://www.keketie.com 。同时本网转载内容仅为传播资讯,不代表本网观点。如涉及作品内容、版权和其它问题,请与本网站联系,我们将在及时删除内容。