生物降解法
有机废气的生物降解处理(也称生物法、生化法或生物催化法),实际上就是 按照废水生化处理的原理来进行的。生物过滤器的发明*早可追溯到1957年Rich¬ard D. Pomeroy的专利(US-Patent No. 2793096 ) o由于用生物法降解废气中的 VOC是在常温、常压下进行,其能耗、操作费和投资相对于其他方法来讲较低, 而且又无二次污染,因此在有机废气的各种净化方法中具有相当的竞争力。
有机废气的生物降解,是利用微生物将废气中所含的有机物氧化(降解)为二 氧化碳和水,即废气中的有机物为微生物提供能量和养分。随着技术的发展,生化 法在有机废气净化中除了可净化有机溶剂或脱臭外,也可除去无机组分,如氨、硫 化氢和含硫有机化合物,因此生化法特别在低浓度的有机废气净化中已不断获得应 用。用于有机废气生化净化的设备,目前主要有三种类型:膜生化反应器,生化过 滤器和生化洗涤器。膜生化反应器主要用于难溶于水、但易挥发的有机化合物的净 化;在有机废气和微生物间设置渗透膜,使难溶于水的有机组分增浓,并进入微生 物中而被降解。但在实际应用中,常见的还是生化过滤器和洗涤器两种。有机废气 的生化处理,如同废水的生化处理一样,要使微生物能发挥作用,而且具有足够的 降解速度,必须满足下面几个条件,即:
①废气中所含的有机物能溶解于水;
②有机物是可以降解的;
③废气温度约在5〜60°C;
④废气中不含有毒物质。
按照废气中所含不同有机物组分,或多或少要有许多种类的菌种参与,例如放 线菌、真菌等。所有这些微生物均被水膜包围,因此有机物必须溶解于水后,才能 被微生物捕获而降解。微生物在适宜的环境条件下将有机物作为养分和能量而生 存、繁殖,并将其完全降解为Co2和H2O如果有机化合物中含有杂原子,如 氮、氯或硫(例如:胺类、氯化炷类和硫醇),则净化程度要视其在水中的溶解度 和可降解性而定。当然,这时会生成无机产物,例如:硝酸盐、盐酸、硫和硫酸等 物质。这些物质可导致过滤材料或洗涤水的pH值的改变,以及在较高浓度时会杀 死微生物。此外,也必须为微生物提供可以生存的条件:pH值约在5〜8,温度5〜6SC,盐浓度较低,以及提供足够的养分和微量元素(氮、磷、钾)等。提高温 度可以加快生物降解速度,但同时也降低了废气中有机组分在水中的溶解度,因此温度升高是受到限制的。
对生化处理极为重要的一个过程是:废气中有机物从气相进到液膜、直至达到 微生物的传质过程。因此,生化装置应尽可能提供较大的相际接触面积。有机废气 生化净化常用的设备如下。
(1)生化过滤器 如图2. 13所示。
在生化过滤器情况下,微生物附着在固体过滤材料上,有机废气从下部进入通过这些过滤材料而先被吸着(吸收、吸附),*后被微生物氧化分解。
生化过滤器常用的过滤材料有:各种不同的堆肥(树皮、残渣堆积物),纤维/ 枯树的泥灰,木屑,椰壳纤维,泡沫玻璃和其他多孔材料,惰性添加物(熔岩灰, 黏土和聚苯乙烯,或这些物质的混合物)等。一般讲,在这些过滤材料中有足够的 无机养分(如氮、磷等)供微生物的生存。如果过滤材料主要是由惰性材料组成, 或当有机废气中含有机物的浓度很高时,则必须添加一定量的养分°
由于有机废气通过生化过滤器时与湿的过滤材料强烈接触,空气被水蒸气饱 和,这样过滤器很快干燥而导致开裂,从而会引起气流分布不均匀。因此,小心地 监控和调节废气的湿度,对生化过滤器的净化效果极为重要。此外,在处理大气量 的有机废气情况下,所需过滤容积很大,通常将过滤器叠成多层式来节省占地面 积。根据不同的过滤材料和废气组成,一般过滤层的高度从0. 8m起,*高至3m。 生化过滤器的阻力大小主要取决于废气处理量和过滤材料本身,通常在500〜2000Pa/m (每米层高)。废气在过滤层中的停留时间大多只有几秒。对于难溶于水 或不易降解的有机物,则停留时间可达30s左右。生化过滤器的尺寸主要决定于废 气的组成,对于臭味强烈的废气可选用空速为100〜250m3/(m3・h)(每立方米过 滤材料、每小时)。对于含溶剂的工业废气,按照不同的降解速度、不同的有机物, 过滤器的处理能力大致在10-100g (溶剂)/(m3- h)o由此可见,生化过滤器的 尺寸很大,例如处理100000m3/h的废气,大约需要过滤器容积为1000m3o为节 省生化过滤器的占地面积,一般都做成多层式,或集装箱叠层式。
(2)生化洗涤器如图2.14所示。
在生化洗涤器情况下,*重要的步骤是洗涤液吸收废气中的有机物。生化洗涤 器分两种类型,即填充床滴流洗涤器和活性污泥洗涤器。
填充床滴流洗涤器通常采用填料塔结构,微生物是挂膜在填料表面上,并同时 用循环水喷淋。有机物的吸收和降解过程都发生在填料表面上;而在活性污泥洗涤 器的情况下,有机物的吸收和降解过程是相互分的。如图2.14(b)所示,洗涤水 和微生物的混合物从顶部用喷嘴将其喷洒到塔中(为增加接触面积,塔中设置多层 挡板),并与底部上升的废气相接触。溶解的有机物则在活性污泥池中降解。空气 鼓入活性污泥池中以便对微生物供氧,并使废气中有机物质解吸。从活性污泥池出 来的废气一般也应回到洗涤器中。通常生化洗涤器中的气速为1〜3m/s,喷淋密度 约为10〜30m3/(m2・h);而水/气比大致在(1,1000)-(1 : 300),这表示若要净 化10000m3/h的废气,则需循环水10~33m3/h。
通常生化洗涤器的容积比生化过滤器小得多,但投资费用特别是操作费远比过 滤器高,因为大量的水要进行循环操作。
根据目前的经验,生化法比较适合于浓度不大于1000〜1500mg/m3 (有机碳) 的有机废气,因为较高的浓度要求装置的尺寸非常大。从目前用生化法净化有机废 气的情况来看,主要用于处理带强烈臭味的气体,例如处理来自堆肥工场、垃圾 场、饲养场、污水处理装置和食品加工厂等产生的臭气;但在许多其他领域中也在 不断获得应用,例如用于处理铸造车间、凝胶体生产厂、印刷厂、涂装车间和木材加工厂等产生的有机废气。
随着有机废气生化技术的不断发展,特别在工艺和设备上有了很大改进,例 如:生化过滤器采用模块结构,单个独立控制湿度、养分,以及集装箱式串联垂直 叠放设计等,从而克服了诸如占地面积大、生物过程难以控制等缺点,当前已有许 多大型生化处理装置获得成功应用,举例如下。
①处理塑料、金属部件喷涂过程产生的有机废气口见
a.用生化过滤器处理塑料部件喷漆产生的废气废气中含有机物的组成用 GC/MS分析系统测定。虽然已知单个组分的可降解性,但并不掌握在混合物条件 下的降解情况。为了确保排放气在达标的条件下尽可能节省装置的投资费用,通过 现场小试验(移动式生化过滤器试验装置)求得生化过滤器的*大容积负荷。用火 焰离子检测器测定生化过滤器前后碳氢化合物的浓度,求得脱除碳氢化合物的净化 效率。通过“Upscaling-Algorithmen”计算软件,将实验中获得的结果放大到工 业装置上,因此可以十分精确地来确定生化过滤器系统的尺寸。装置的操作数据 如下。
b.用洗涤器/生化过滤器处理喷涂金属部件产生的废气该过程是先用人工方 法喷涂金属部件,然后再继续用自动喷涂作进一步加工。因此,排出废气的浓度波 动很大,在每隔几分钟(手工操作时)出现高浓度的峰值,之后又恢复到浓度 100mg/m3左右。在本案例情况下,先借高效填料洗涤塔用水吸收可溶解的有机 物,并使废气增湿。洗涤器起到缓冲作用,即高浓度时被吸收一部分,而当废气浓 度低时,循环水中溶解的一部分有机物被解吸,重新又回到废气流中。这样可使进 入生化过滤器的废气浓度相对稳定。生化过滤器的类型也是按模块、集装箱式设 计。装置的操作数据如下。
上采用上述模块、集装箱式的生化过滤器,由两排共2X8个集装箱叠起组成的 一套生化处理装置。实际布置集装箱的基础面积约70m2,可设计有效过滤器面积 67.5m2,故整个生化装置的总过滤面积约540m2,相当于整个过滤器面积负荷约 185m3/ho有机废气先经干式除尘、增湿后,再依次通过集装箱式生化过滤器后排空
主要操作数据如下。
除上述例子外,生物降解法还用于装饰纸张浸渍过程和显像管生产中的清洗过
程所排放的有机废气净化。
低温等离子体法
等离子体是指处于电离状态的气态物质,它是由大量带电粒子和中性粒子所组 成,在电磁力作用下粒子的运动和行为以集体效应为主的体系,并呈电中性。在放 电设备中产生的由电子、离子和中性粒子所组成的电离气体就是等离子体,通常它 与物质的气、固、液三态并列,称等离子体为物质的第四种形态。通过气体放电或 加热方法(温度在25OO°C以上)从外界获得足够能量,而使气体分子或原子中轨 道所束缚的电子变为自由电子,即形成等离子体;但这里讲的是在常温、常压下采 用高压脉冲电晕放电产生等离子体,所以也称低温等离子体法。
采用等离子体法净化含VOC废气的作用机理,大致可概括为以下几点〕.
①空气分子或原子通过电子的获得或失去而被电离,即离子化。
②基于周围环境能量的提高(在电场中),原子或分子的外层电子起变化,即 迁移到靠近原子核的一个层上,同时产生光。
③在电场内,空气的组成部分转变为强氧化物,例如臭氧、水分变为OH- o
④在电场内,可以提高对化学反应起到关键作用的原子或分子的平移位能, 即激活过的气体组成部分比未激活的具有更强的反应能力。这些活化的(自由基 的)空气组成部分与气体中可氧化的物质反应。
等离子体有不同的类型,即电中性、非电中性、高密度、低密度、高温、低温 等离子体。在有机废气净化技术中,涉及的是低温等离子体技术,也称非热力等离 子体技术(Non Thermal Plasma Techniques, NTP) o分子在强的交流电场中激 发,使气体分子的振动状态在理论上相当于加热到几千摄氏度,而实际上其温度并
无变化。
目前,等离子体法在工业应用中主要有两种工艺:一是通过脉冲电晕放电;二 是所谓的介电质阻挡放电。另外还有电子辐射反应器或纳米秒范围内的脉冲放电 等,近年来已获得很大发展,特别是用于脱臭和火力发电厂的脱硝。
在有机废气净化的实际应用中,等离子体主要是通过高压交流电场来实现的。 电场的作用是产生非常不同的能量变化,而使气体分子(原子)电离、离解,从而 在常温下提高了原子和分子的平移位能或使其具有较高的氧化势能。在强电场的作 用下,气体分子受到激发而产生大量自由电子并获得能量。当电子的能量与C一 H、C—C、C-C键的键能相等或接近时,可使这些碳氢化合物开键并破坏其结 构;此外,在强电场作用下产生的臭氧也增强了氧化力,这样废气中的碳氢化合物 *终被氧化为无害的co2和H2O0
在废气净化的实施过程中,可以将废气直接引入等离子体反应器中(直接操作 法),或先将新鲜空气引入等离子反应器 应空间中混合、反应(间接操作 法)。目前在工业上用得较多的是 介电质阻挡放电法。在电容器式反 应器情况下,通常要用400〜20000Hz的交流电进行周期性的充 电和放电。电容器式反应器有不同 的结构类型,例如板式、管式、棒 式等。图2. 15表示了用于低温等离 子体的一种多层板式电容器原理。 介电质的材质常用堇青石陶瓷和莫 来石陶瓷,目前也有用氧化铝或二 氧化钛做成。
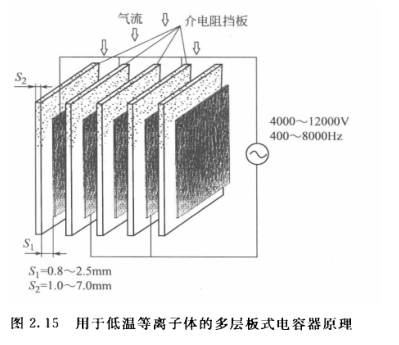
*初有机物在等离子体反应幕 中氧化所需操作费很高,而目前已降到技术上可以承受的能耗,例如脱臭,每千克臭气的平均能耗约为15kW・h, 而处理氯化炷类则有些能耗尚高于100kW - h/kgo就目前有机废气净化的工业应 用而言,其能耗大致为1.5〜5kW/1000m3 (有机废气〕。由于废气在处理过程 中的温度几乎没有变化,因此能量消耗很低。
当有机废气的净化率要求很高时,例如〉99.9%,通常在用等离子体法处理后 再连接一个催化反应器。按照废气所含有机物和湿度的不同,可用Fe、Cu、Mn、 Cr氧化物催化剂,有时也用贵金属催化剂(例如Pd、Pt),或者例如在处理含氟、 氯炷有机物情况下,可采用混合催化剂系统。这种方法的流程如图2.16所示[⑷。 在第*级中,气体分子在强交变电场中被激发,然后进入环境温度下(或相应的废 气温度)的催化反应器(在一般有机废气的催化净化情况下,必须将废气预热到约350°C后才能进行催化反应),使其转化为CO2和H2C),而无其他副产物。
应该指出,当需要处理的废气量大到不可能全部输入等离子体发生器时,通常 只将一部分废气或新鲜空气进入其中(其量约为废气总量的1。%),使这部分气体 激活,然后再混入总的废气流中;当然,关键是要有足够的气体分子被激活。如前 所述,这种方法称为间接操作法。全部将废气直接输入等离子体发生器中,当然效 果更佳,因为除了气体分子的激活外,气态有机污染物与电子的直接接触,使一部 分有机物早已分解°
与其他方法相比,由于等离子体法在净化有机废气特别是在低浓度、脱臭方 面,它具有能耗低、效率高、设备简单、操作可靠等优点,所以已成为有机废气净 化中的一种新方法。因此,目前对低浓度VOC废气的净化,特别是在脱臭方面已 有不少获得成功应用的例子。有关低温等离子体法在有机废气净化中的原理及相应 装置的优化。
①处理饲料生产过程中产生的臭气。
废气处理量:70000m3/h,含尘量相对较高,可至40mg/m3。
采用等离子体法和间接操作方式,即先将新鲜空气引入等离子体反应器中,激 发后与废气混合、反应。因为含尘量高,如连接催化反应器,则必须设置费用较高的除尘器。
②处理纺织工业中火焰黏合设备(用于泡沫衬里织物)产生的废气。
废气中含氢氧物和VOC,采用板式电容器作为等离子体反应器,共8组电极 板,每组功率至1. 5kW。
③处理纺织工业中涂层设备产生的酚醛树脂、石蜡类臭气。
采用等离子体法+催化反应
废气量:15000m3/h,废气温度高至300°C ,回收热量用于干燥过程和催化 反应。
④处理芳构化和石油精炼过程产生的废气。
废气量:<11000m3/h
低温等离子体法+催化反应:臭气从0. 7X106 GE/m3降到VlOOOGE/m,,净 化率>99. 99%
低温等离子体法+分子筛:臭气从50000GE/m3降到V 1500GE/m3,净化 率V99. 6%
⑤处理熔炉中锌板涂层熔炼后产生的裂解废气。
废气量:11000m3/h
废气中主要含芳炷、苯等VOC气体,浓度V700mg/m3,大多为苯(400mg/ m3) o
低温等离子体法+催化反应:净化率>99.3%,催化反应温度为180〜220°C (若不用等离子体法,反应温度为330。0。
⑥处理饲料生产过程中产生的臭气。
采用等离子体法
废气处理量:80000m3/h
废气中含VOC气体V50mg/m3,温度V45°C,相对湿度V 60%,处理后 臭气 V5000GE/m3。
低温等离子体法在香料、香精生产中脱除排放气中V()C的 应用,因为过量的香气对人的呼吸系统也会造成强烈刺激。该文献将低温等离子体 法与热力燃烧、催化燃烧、蓄热式热力燃烧、生化处理和分子筛吸附等方法在投资 费用、操作费、二氧化碳的排放三个方面作了比较后认为:在香料、香精工业生产 中的废气处理量为50000m3/h, VOC浓度约小于1 OOmg/m3的条件下,低温等离 子体法是*佳的选择。
此外,紫外线灯(汞灯)也可用作*简单的等离子体源。在一定频谱范围内, 在技术上可以用来激发气体分子,使有机物氧化为无害物质。这种设备要求低又简 单,也可与活性炭或分子筛吸附联合使用,达到更高的净化效果。因此,常用于室 内空气净化和脱臭。
光催化氧化法
众所周知,紫外线是由电磁波组成,其能量与波长直接有关,波长越短,能量 越大。当紫外光灯发射出不同的波长时,若要使废气中的VOC借紫外光直接通过 自由基链锁反应降解,则VOC也必须能吸收这类波长,即紫外光灯的*大发射要 与VOC的*大吸收相一致。这种借紫外光产生的反应称为光氧化或光解。光解作 用不是净化VOC污染的唯一效应。若紫外光发射的强度越大,则空气中的氧极易 分解为臭氧;产生的臭氧也分解为自由基,从而加剧了光解过程;此外,空气中的 水分在紫外光作用下也可分解为OH-,同样也参与VOC的氧化。因此,在紫外 光的作用下,通过上述几种效应的叠加可以产生大量活性自由基,从而高效地使 VOC降解。如果后续催化反应,即光催化氧化,则VOC的净化效果更佳。
光催化氧化法是借催化剂具有光催化作用的性能,将吸附在催化剂表面上的 VOC氧化为CO2和H2。。通常用于一些比较容易氧化的有机化合物。如前所述, 在紫外线的照射下不断产生大量活性的自由基,使大部分VOC降解;而光催化剂 可加速化学反应有助于有机物进行降解反应;同时还有消毒、杀菌作用。经典的光 催化剂都是半导体,其中*有效的光催化剂是TiO2,还有ZnO、SnO2. Fe2O3. CdS、ZnS、WO3、PbS等。由于TiC)2对紫外光线有很高的吸收率,还具有较高
的催化活性和化学稳定性,以及无毒而价廉等优点,所以应用*广。
光催化氧化法的反应机理如下「皿⑵」根据半导体的电子结构理论,光催化性能 取决于晶粒内的能带结构,能带结构由一个充满电子的低能价带和一个空的高能导 带所构成,两者间由禁带分开,其能差即为带隙能。在光照射半导体光催化剂的情 况下,当吸收一个能量大于或等于其带隙能的光子时,电子会从充满的价带跃迁到 空的导带,而在价带留下带正电的空穴。光致空穴具有很强的氧化性,并能夺取吸 附在催化剂颗粒表面的有机物中的电子,使本来不吸收光而无法被光子直接氧化的 物质,经光催化而被活化、氧化。Ti()2经光激发后产生高活性光生空穴和光生电 子,并经一系列反应后生成大量高活性的自由基,因而TiC>2表面的羟基化是光催 化氧化VOC的必要条件。此外,VOC光催化降解的速率主要取决于催化剂吸附 VOC的性能和光催化反应速率,因此寻求对V()C具有高的吸附效率和较快降解 速率的光催化剂是极为重要的。
目前该方法主要用于室内外VCC污染的净化和脱臭,例如:用于医院、宾 馆、车站、机场、博物馆、厨房、污水处理、发酵和食品加工等场所排放的臭气净 化。此外,这种Ti()2光催化技术,一方面利用Ti()2具有极高的折射率已广泛用 于涂料、塑料和建筑材料中;而另一方面则利用纳米TiCh的量子尺寸效应来提高 它的光催化活性,以及光催化的除菌性能,早已成功地用于陶瓷、纺织品、化妆品 (即所谓抗菌陶瓷、抗菌纤维)等领域中。当然,用紫外线处理的光氧化法对某些 有机化合物也只能达到部分氧化;另外,如果有机物容易聚合并沉积在灯管上,则 会影响效果;该法的能耗还是相对较高。
通常紫外光发射器分低压和高压两类。前者产生离散的紫外线,波长在185〜254nm范围,这种灯主要用于消毒,一般功率在10〜400W;后者产生拟连续发射 光谱,功率在1000〜32OOOW。
21世纪初,尤其在日本,应用光氧化和催化氧化技术的组合(例如与活性炭 吸附相结合)已开发了相应的产品,并获得成功应用,例如,2003年用于德国 Krauss公司的工厂溶剂排放处理,室外机的处理量达30000m3/h;而2004年同样 也是用于德国SRI Radio System的空调脱臭,室内机,两个系统处理量分别为 40000m3/h 和 50000m3/hL2。」。又如文献[22]报道,德国 IBL Umwelt-und Bio- technik GmbH公司开发的紫外线反应器已用于:①喷漆车间的废气处理,废气处 理量为55000Nm3/h,废气中V()C的成分主要是丁酮、苯和甲苯,总有机碳浓度 为150mg/Nm3;②橡胶生产过程的排放气,废气处理量为12000Nm3/h,废气中 VOC的成分主要是丁酮、苯和甲苯,总有机碳浓度为750mg/Nm3;③处理含氯苯 废气,废气处理量为2000Nm3/h,总有机碳浓度为225mg/Nm3°
燃烧法
有机废气净化的燃烧法是基于废气中有机化合物可以燃烧氧化的特性,其目的 是:通过燃烧将废气中可氧化的组分转化为无害物质,在废气中含纯碳氢化合物的 情况下,即转化为CO?和H/)。当然,由于有机废气中所含有害物质组分的不同
(例如:可以是纯碳氢化合物,含硫、氟、氯等炷类物质或含尘等废气)、浓度不同 (废气含有机物的浓度可以从感觉到的气味,每立方米几毫克到几百克甚至更多)、 燃烧过程温度的控制因素的不同以及不同的燃烧方式等,可能存在各种氧化/还原 反应和热分解反应。此外,燃烧过程始终伴随热量的产生,因此不同的热量回收和 利用方式,也构成了不同类型的燃烧净化方法和燃烧净化装置。
从有机废气的来源和可燃物的爆炸极限角度讲,有机废气净化技术中所要处理 的VOC废气可如下来分类。
其一是从有机废气的来源分类。
①过程释放气 例如:在生产过程中未反应的原料气、副产气体以及为安全 生产必须排放的可燃气体(如石油、天然气开采等设置的火炬)。这类过程释放气 的特点是所含有机可燃物的浓度相对较高,大部分可直接回收再利用或回收其 热能。
②排风气 由于生产过程中所用的有机物(特别是溶剂)不可避免地通过挥 发、泄漏而释放VOC,以及煤矿的煤层气(俗称瓦斯,主要是甲烷),为健康和生 产的安全必须用风机将其通风排出o这类排风气的特点是所含有机可燃物的浓度相 对较低、甚至极低,但风量很大,而且主要是空气,有机物的回收或热能利用都比 过程气难。
其二是从可燃物的爆炸极限角度分类。
①排风气 VOC浓度低于爆炸下限。
②可爆炸的有机废气VOC的浓度在爆炸浓度范围内,随时可着火。处理这 类废气必须有相应的安全措施。
③富气 VOC浓度高于爆炸上限。这类废气由于其热值相对较高,可直接作 为燃料用。
应该指出,除上述分类外,在有机废气净化技术范围内,还有一种要处理的有 机废气例如气味或恶臭,或称贫气,其浓度比一般生产过程的排风气还要低得多; 另外,如垃圾贮存、填埋产生的沉积气,其主要成分是甲烷,均属贫气一类。
有机废气净化的燃烧法主要分三种类型,即直接燃烧、热力燃烧和催化燃烧。 当废气中VOC浓度很高时,可把废气当作燃料来燃烧,所以称其为直接燃烧;而 在热力燃烧和催化燃烧情况下,所处理的废气中可燃物的浓度太低,必须借辅助燃 料来实现燃烧,故称为热力燃烧,也称后燃烧、无烟燃烧。在有机废气净化中的催 化燃烧,当然也属于热力燃烧,只是因为具有催化反应特点而单独分出。催化燃烧 的目的是:利用催化剂的催化作用来降低氧化反应温度和提高反应速率。为了尽可 能节省辅助燃料和充分利用有机物燃烧时产生的热量(用于预热废气),热力燃烧 和催化燃烧按不同的回收热量方式又可分为:不回收热量的热力燃烧,带间壁式换 热器的热力燃烧,蓄热式热力燃烧,不回收热量的催化燃烧,带间壁式换热器的催 化燃烧和蓄热式催化燃烧。在有机废气净化中,通常将用于预热废气的换热器分为 蓄热式换热器(也称交流换热器,Regenerator)和间壁式换热器(也称同流换热 器,Recuperator) o常见的间壁式换热器例如有管壳式换热器(也称管束式或列管 式换热器)和板式换热器。对应这两种换热器的净化装置,在文献中经常出现蓄热 式热力氧化器(Regenerative Thermal Oxidizer, RTO)、带间壁式换热器的热力氧 化器(Recuperative Thermal Oxidizer)和蓄热式催化氧化器(Regenerative Cata¬lytic Oxidizer, RCO) o
在绝大多数处理有机废气的场合,废气中VOC的浓度一般都很低,而风量相 当大。因此,往往因为回收废气中的有机溶剂在经济上不合算,或难以使回收后的 溶剂重复使用,以及在回收过程中可能产生二次污染等问题,才采用燃烧法来净化 有机废气。
(1)直接燃烧法 直接燃烧是将有机废气当作燃料来燃烧。通常适用于废气中 所含可燃物的浓度非常高,其浓度一般高于爆炸浓度上限,而且它具有相应高的燃 烧热值,即不需添加辅助燃料也能维持燃烧所需的温度。直接燃烧时产生明亮的火 焰,故也称火烟燃烧。在一般含碳氢化合物的有机废气情况下,直接燃烧后的产物 主要是C()2和H2OO这里也要提及的另一种情况,即虽然废气中的可燃物浓度很 低,但有时也可将其送到生产中已有的燃烧室中直接燃烧,例如将有机废气代替锅 炉燃烧室所需的空气;否则只能采用热力燃烧,即添加辅助燃料来燃烧。直接燃烧 法不适用于大风量、低浓度的有机废气净化。
要实现完全燃烧的先决条件是:除了要有足够高的温度外,还要使可燃物与空 气获得良好的混合,以及具有足够的空气量(氧气)。当空气量不足时,则燃烧不 完全,在废气中还存在未燃尽的有机物;若空气过剩量太高,则温度降低,燃烧同 样也不完全或低于着火点而熄火。此外,要使一种可燃物/空气混合物能着火,可 燃物的浓度必须在着火界限范围内(即爆炸极限浓度范围内)。着火下限表示可燃 物的量不足,着火上限表示可燃物过剩。这表示:在采用直接燃烧法时,若可燃 物/空气混合物的浓度处于爆炸极限范围之内,则存在易燃、易爆和火焰可能经管 道回火的危险性,因此必须采取相应的安全措施;若废气中可燃物的浓度超过爆炸 上限,则必须补充空气,借以保证有机废气在氧量充足的条件下达到完全燃烧。若 浓度处于爆炸范围内,一般可用空气或惰性气体将其稀释至爆炸下限以下,但此时 也必然增加了辅助燃料的消耗。
直接燃烧法的火烟燃烧温度一般约在1100°C左右。
直接燃烧法常用的设备有炉、窑以及像炼油和石化工业中常见的火炬。应该指 出,火炬燃烧只是生产工艺过程中的一种安全措施,火炬是敞开式的燃烧器,因此 燃烧是不完全的,它不仅造成燃料能量的损失,而且还会产生大量有害气体和烟 尘,以及热辐射,从而污染环境,应尽可能回收利用。
(2)热力燃烧法因为有机废气中所含可燃物的浓度极低,不能着火和依靠自
身来维持燃烧,所以必须借辅助燃料燃烧产生的热量来提高废气温度,使废气中 VOC氧化并转化为无害物质。经典的有机废气热力燃烧设备主要由辅助燃烧器和 燃烧室组成。当燃烧室的温度达到可以点燃有机废气时,才将废气引入燃烧室中进 行氧化燃烧,然后净化后气体经烟囱排入大气。根据废气中空气含量(即氧含量) 的大小,采用不同的燃烧器:若废气中氧大于16%,则用配烟燃烧器;若小于 16%,则用离烟燃烧器,即必须补充助燃空气。为保证VOC能完全氧化,废气在 燃烧室中要有足够的停留时间,一般为0.3〜0.5s;以及足够高的温度,一般为 720〜850°C;当然也有高温热力焚烧炉,温度可至850〜1250笆;这要视VOC的 种类、组成及排放气应达到的指标而定。
上述经典的有机废气热力焚烧炉,由于结构简单、投资费用少、操作方便,而 且几乎可以处理一切有机废气和达到法规的排放要求,因此在20世纪90年代以前 应用极为普遍。但是,这种焚烧炉的燃料消耗高也不回收热量,极不经济,所以目 前已被带有热量回收系统的热力燃烧装置所代替.
(3)蓄热式燃烧法 在热力燃烧装置的操作费中,主要部分来自辅助燃料的消 耗。在许多情况下,常用废气预热器来降低燃料消耗,即通过冷却净化气来预热废 气,使得达到燃烧室温度只需少量燃料。当预热温度足够高时,如果废气中可燃物 的燃烧热值足以达到反应温度而不需添加辅助燃料,则称为自供热操作。但是,如 果废气中可燃物的含量很低,这就表示要求选用更高的预热温度。这对常用的间壁 式换热器而言,无论在结构上或是在材料上都难以做到。为此,借鉴多年来在冶 金、化工和工业炉等领域中业已获得成功应用的蓄热炉经验,将其用于有机废气的 净化,即蓄热式热力氧化器。
典型的蓄热换热方法,一般至少要两台换热器来实现加热和冷却周期的切换, 才能使过程连续操作;当然也可用旋转蓄热式换热器同时连续地进行加热和冷却。 常用的蓄热体有:陶瓷散堆填料(例如:矩鞍环填料)和陶瓷规整填料(例如:蜂 窝填料).操作温度一般为800〜850C,可处理浓度低、风量大的有机废气。
在有机废气净化的诸方法中,蓄热燃烧法(RTO)应用较广,一方面是因为 只要充分满足燃烧过程的必要条件,燃烧法可以使有害物质达到完全燃烧氧化而变 为无害物质,即达到规定的排放要求;另一方面,燃烧法的经济性主要取决于过程 热量的回收和利用程度,特别在RTO的情况下,由于过程的热效率很高(一般都 在95%以上),通常只需补充少量辅助燃料;而当废气中有机物浓度达到一定值时 (一般大于2〜3g/m3,视有机物的种类、组成而定),即可实现自供热操作,而不 必添加辅助燃料。此外,RTO的操作维护十分简单、可靠,不需经常更换零部件 和使用寿命较长。此外,有些净化方法在处理后,常常还要用RTO作*后处理才 能达到排放要求。当然,其缺点是:容积较大,一次性投资费用较高。
(4)催化燃烧法采用催化剂可以降低有机物氧化所需的活化能,并提高反应 速率,从而可以在较低的温度下进行氧化燃烧,使有机物转化为无害物质。在催化 燃烧时,一般都采用固体催化剂,因此涉及的是非均相催化反应。常用的催化剂主要是载体催化剂,即将催化剂的活性组分沉积于陶瓷或金属载体上。有机废气催化 燃烧时所用的催化剂大多以陶瓷材料作为载体,并做成颗粒、圆柱或空心圆柱体和 蜂窝等形状。常见的催化剂有:贵金属催化剂,如钳、钮、钉等,但价格昂贵和耐 中毒性差(为减少贵金属用量,也有用Pt-Al2O3);非贵金属氧化物催化剂,如 铜、铭、钻、镣、镒等氧化物;以及稀土元素氧化物。有机废气催化燃烧所用的设 备类型主要有固定床和流化床两种,并在其中设置间壁式换热器来预热废气;也有 在蓄热换热器上添加催化剂,借以提高系统的热效率。在考虑催化装置时必须注意 下面三个参数。
①空速 即每小时、每立方米催化剂的废气处理量,这个数值决定了装置的 尺寸,通常空速在10000〜20000Nm3/(m3・h),对于难分解的有机物选用空速小 于 5000Nm3/(m3・h)o
②温度温度高低主要取决于空速及需要除去有机物的性质,应确保有机物 的完全氧化,一般在200〜450C范围内。
③压降 气速大小、催化剂的形状和结构以及床层高度决定了压降的大小。 对于颗粒状催化剂,其压降一般在1 OkPa/m;而蜂窝催化剂的压降约为IkPa/m。 为保证通过床层时具有良好的气体分布,必须有一个*低的压降;但从节能要求, 压降应尽可能低。
虽然催化燃烧与非催化热力燃烧相比其氧化温度明显要低得多, 转化操作更为经济,但其缺点是:对所处理的有机废气有一定要求, 催化剂中毒、抑制反应、堵塞或覆盖催化剂活性中心的物质;此外, 和经常需要更换也制约了其应用。
版权声明:本网注明来源为“乐发环保”的文字、图片内容,版权均属本站所有,如若转载,请注明本文出处:http://www.keketie.com 。同时本网转载内容仅为传播资讯,不代表本网观点。如涉及作品内容、版权和其它问题,请与本网站联系,我们将在及时删除内容。